When considering the thickness of materials in various industries, the term gauge often comes into play, particularly in contexts involving metal, wire, and needles. Understanding the conversion from gauge to inches is critical for professionals who demand precision in their work, from craftsmen and jewelers to build contractors and medical professionals. The term 18 gauge is one of the most common references, yet it requires clarification, especially in relation to its measurement in inches.
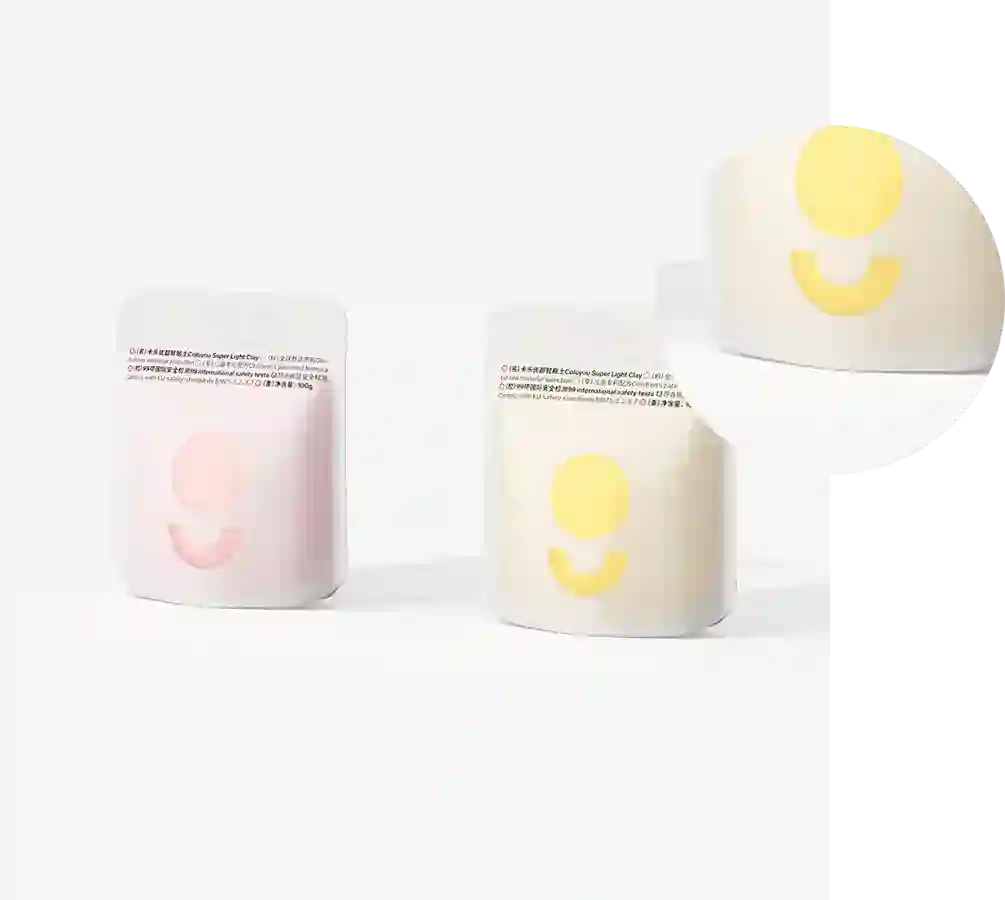
Starting with the basics, the gauge system is used to denote the thickness of various materials. However, the challenge arises from the fact that the gauge system doesn't have a universal standard and can differ based on the material being measured. Here, we are specifically focusing on metal and wire thickness, which is crucial for applications ranging from construction to automotive manufacturing.
For metal, particularly sheet metal, 18 gauge typically corresponds to a thickness of 0.
0478 inches (1.214 millimeters). This measurement is vital for ensuring structural integrity and performance. In the automotive industry, for example, using the correct gauge can influence vehicle safety, aerodynamics, and fuel efficiency. When body panels are too thick, it could lead to increased weight and reduced fuel economy; too thin, and it may compromise safety and structural integrity.
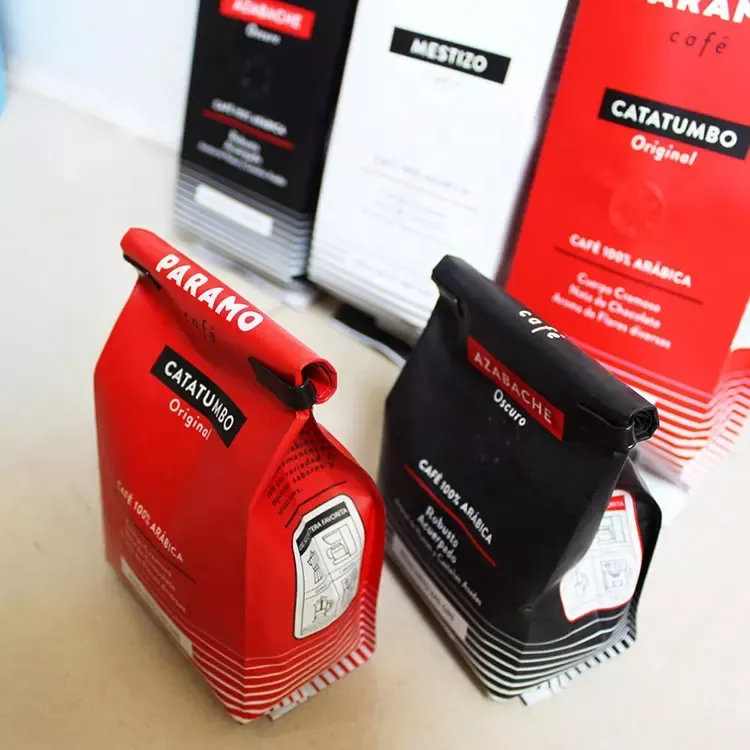
In the realm of wire, the term 18 gauge pertains to its diameter, which is approximately 0.0403 inches (1.024 millimeters). This specification is crucial in ensuring proper electrical conductivity and load capacity. When wiring a house, selecting the correct wire thickness can prevent overheating and potential fire hazards. Furthermore, in electronics, the accuracy of these measurements ensures devices operate efficiently without risk of short-circuiting.
For medical professionals, particularly those specializing in surgery and phlebotomy, needle gauges are critical. Here, 18 gauge needles are typically used for blood donation and transfusions, with an external diameter of about 0.050 inches (1.27 millimeters). This knowledge allows for the selection of appropriate needle sizes to ensure patient comfort while maintaining procedural effectiveness and safety.
18 gauge to in
It's essential to rely on authoritative, professional resources to obtain precise gauge to inches conversions. Engineers often refer to standards like those provided by the American Iron and Steel Institute (AISI) and the American Wire Gauge (AWG) system. Consulting reliable publications and industry manuals ensures that professionals are using accurate, consistent measurements tailored to their specific needs.
The trustworthiness of measurements and their sources is paramount. Manufacturers must adhere to stringent regulations and quality controls, ensuring their materials are accurately labeled as per gauge specifications. Failure to do so can result in structural weaknesses, electrical faults, and compromised safety, underlining the importance of dependable gauge-to-inch knowledge.
A comprehensive understanding of gauge measurements not only enhances product quality and safety but also reinforces professional authority and expertise. Mastering this conversion indicates a thorough awareness of industry standards, necessary for making informed decisions in project planning and execution. As technology progresses, staying updated on these standards and methods through continuous professional development is vital for maintaining and growing one's expertise and trust in their field.
In conclusion, the conversion of 18 gauge to inches extends beyond mere numbers; it embodies the integration of precision, safety, and quality in every industry relying on this measurement system. Being versed in these conversions reflects a commitment to excellence and reliability, key factors that build a distinguished reputation in any professional field.